Conveying and Spreading “Panasonic’s Value” to the World—Sharing Konosuke Matsushita Vision That Has Taken Root in the Hearts of Scholarship Alumni
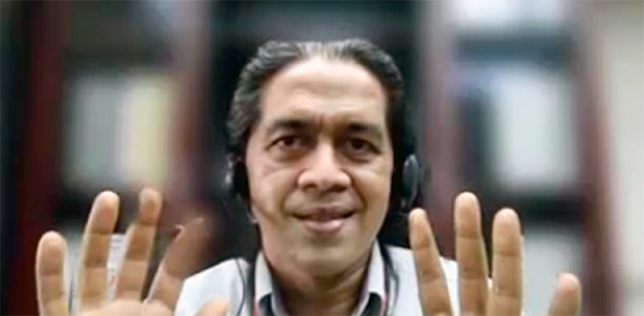
○Mr. Muzafar Bin Mohd Yusoff
Nationality: Malaysian
Current country of residence and job type: Malaysia, Panasonic Appliances Air-Conditioning Malaysia Sdn. Bhd.
Awarded in 2000 -> Chiba University, Graduate School of Science and Technology, Intelligence Information Science -> In 2003, after completing his master's degree, he joined Matsushita Electric Industrial Corporation Japan. After being involved in Seihin Shinsa (Product Evaluation), he worked as an expert to support quality management systems (QMS) and quality assurance governance, as well as overseas technical regulations -> In 2019, he joined Panasonic Appliances Air-Conditioning Malaysia Sdn. Bhd.
After studying abroad, Mr. Muzafar Bin Mohd Yusoff secured his employment in Japan, where he worked for about 20 years in roles related to product quality at the Panasonic and Appliances headquarters. Those worksites placed him closest to the heart of the philosophy of Panasonic’s founder, Konosuke Matsushita— safe, secure, durable, and user-friendly products. But Mr. Muzafar believes there's more to it than that. He refers to this something more as the “Panasonic’s value,” which has been imparted to many alumni who studied in Japan through the Panasonic Scholarship. Now, Mr. Muzafar has taken a new step to spread “Panasonic’s value” to the rest of the world, and he wanted to share and realize the possibilities that he sees coming in the future.
A desire to spread the value of Panasonic to the world that couldn’t be done from Japan
In 2019, Mr. Muzafar returned to his home country which is Malaysia. Currently, he is responsible for quality planning at Panasonic AP Air Conditioner Malaysia Sdn. Bhd. (PAPAMY), a manufacturing base that exports products to more than 120 countries worldwide. He decided to leave Panasonic headquarters, where he had worked for about 17 years, and return home for the education of his young children and to realize a certain personal desire of his.
“I learned many things in Japan and at Panasonic. Those things have their roots in Japan's unique culture and code of conduct, which is different from that of Malaysia, where I was born and raised, Australia, where I first studied abroad, or any of the other countries in the world I visited after joining Panasonic. For example, the attitude of working without being constrained by set times and understanding things deeply; the consideration that goes into everything from product design to manufacturing, with the idea that the goal of one's work is the satisfaction of your end-users; and the norm of always adhering to every single thing that has been decided. For those born and raised outside of Japan, those things are suffocating or inexplicable. But they really aligned with my personality. Ever since I was little, I wanted to be different, and the things I would say or do were outlandish to the point of annoying my father. I even thought I was a “unique person” because of that. However, when I came to Japan, I was surprised to find that in both my studies and work, there were many more “strange people” besides myself. At the same time, I thought the way Japanese people approached things really suited me.”
After graduating from university in Australia, Mr. Muzafar, wanted to further his education and was planning his next study abroad. He had two options: Germany or Japan. Both Japan and Germany held great promise as technologically advanced countries for Mr. Muzafar, who wanted to advance in the field of technology. However, his desire to do things differently from others led him to decide that Japan was the only option for him. He says that his childhood experiences were also a factor in his decision. Because Mr. Muzafar’s father worked for a Japanese company, he had experiences interacting with his father’s Japanese colleagues from an early age.
“I still remember how surprised I was when I visited a Japanese home. The house was neat and tidy, and the way they behaved within their daily life was unique. Something was different. I received a toy that the child in that house had used, but it had been treated with such care that it seemed brand new. I wondered why things were so different, but now I know why. I realized that 5S activities were thoroughly employed in that house.”
“5S activities” are activities to ensure that products and services are sorted, set in order, shined, standardized, and sustained to improve Q (quality), C (cost), and D (delivery time). Mr. Muzafar, who would later join Panasonic and worked extensively on quality-related matters, apparently felt that the standard of quality required for Japanese products are rooted in Japanese culture.
“At Panasonic, I was responsible for inspecting almost every product and played a role in maintaining quality standards for exports overseas. I would set standards, create mechanisms, and stick to those standards and mechanisms. However, even when I communicated those rules to countries and people outside Japan, that alone would not be enough to ensure that the value of Panasonic products reaches users outside of Japan. Panasonic’s value comes from Japanese culture. I can understand that culture, translate and convey it in English so that it can blend in with the cultures of people from other countries. When I wanted to give back to Panasonic, which has made me feel worthwhile, fulfilled, and allowed me to experience a “different and special way of living” through many years of service, I was convinced that spreading the high value of Panasonic was something I could do precisely because of who I am. But there is a limit to what I can do to accomplish that while being in Japan. I knew that I had to leave the country. Returning to Malaysia was also the first step of that new challenge for me.
Thinking deeply about the people who use to deliver good products
After being awarded the Panasonic Scholarship, studying abroad at Chiba University, and graduating from a master's degree program there, Mr. Muzafar only wanted to find a job in Japan, and only at Panasonic. This was due to his admiration for Panasonic’s founder, Konosuke Matsushita, who Mr. Muzafar was able to deeply understand through the Panasonic Scholarship.
“My parents had several home appliances made under what was then the “National” brand name. All of their appliances were durable and long-lasting, and ever since I was a kid, I thought they were a company that makes amazing things. Konosuke Matsushita left us with the words ‘Make people before products.’ But I thought that regardless of the country or culture, companies ‘use people to make products,’ and that’s what work was all about, so I was deeply impressed by Konosuke Matsushita’s philosophy. It made me wonder if those home appliances started with the development of people. I was also curious about what kind of company it was, and at that point, I couldn’t imagine myself working anywhere else but Panasonic.”
After Mr. Muzafar’s wish came true and he joined Panasonic, an unexpected job awaited him. Mr. Muzafar, who had studied information engineering at university, was assigned to the internal IT system department.
“I was in a tough spot. I was good at enhancing the performance of actual equipment that was in front of me at the on-site lab, but I was not good at anticipating, imagining, and designing systems. I wanted to contribute to the Panasonic that I admired, so I asked myself what my strengths were. Then I thought that I would take advantage of my character as a ‘strange person’ and took training on quality. When I did that, I got an offer from the Quality Division. They said that they needed the perspective of a non-Japanese person to consider the quality of products for export. I was delighted to receive that offer. At the same time, I was also surprised. My new assignment was in Seihin Shinsa (Product Evaluation). And as far as Seihin Shinsa was concerned, I knew it was an important place for Konosuke Matsushita and the history of Panasonic.”
In December 1945, shortly after the end of World War II, Konosuke Matsushita established a “Product Inspection Institute,” and the purpose was to improve the technology and quality of his products, he decided that “anything that does not pass through the Product Inspection Institute will not be released to the market.” The reason for this was that he wanted his employees to understand that products should not be sold at a high price to make a profit, but that there was value in the excitement of being recognized for the hard work and effort that goes into production.
As the first foreign employee in Panasonic’s history to be assigned to the Quality Division, Mr. Muzafar began to exceed expectations. The products that Muzafar screened were ones that always broke, did not pass Seihin Shinsa , and were suspended from shipping. Talk of this quickly spread throughout the company.
“The seal that I use to stamp my name in place of a signature is engraved with Japanese characters that read as ‘Muza.’ When the heads of each business division saw all the documents for suspended shipments, they started saying, ‘Who is this Muza?’ I longed to achieve “unbreakable home appliances,” and wanted to be in charge of manufacturing such products, and here I was, putting down stamps to suspend shipments in Seihin Shinsa, which can be said to be the headquarters of Panasonic. I was surprised but also proud of what I was doing. Many people would ask me, ‘Mr. Muzafar, why do products break when you touch them?’ But when I explained why, everyone understood and agreed.”
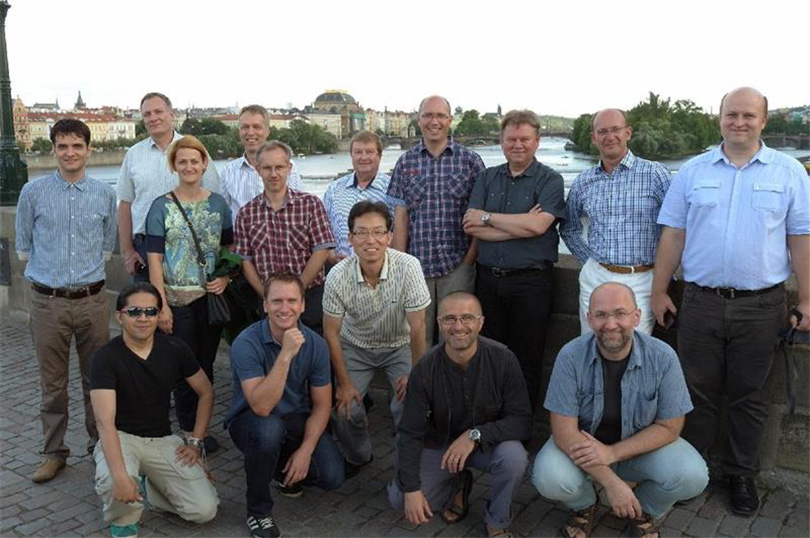
Mr. Muzafar participated as a Japanese representative (lecturer) in a training session for small group leaders at a Panasonic manufacturing base in the Czech Republic. He made great efforts to communicate with representatives for each country.
Mr. Muzafar first imagined how a product would be used in a country with lifestyle habits that differ from Japan. If you're an American used to big refrigerators, the strength that you use to open and close the door is different. He also did various simulations of how the products are used, recalling the different ways that students from different countries cooked when he lived with them in the foreign student hall in his university days. All of the issues that came up were not anticipated during the product design stage. Next, Mr. Muzafar would go to an electronics retail store to observe how the Japanese use it. He would also try products from other companies and verify the differences.
“For example, if you do a lot of housework, how an object feels to touch is important, even when it comes to pushing a button. It’s better to have a touch-sensitive button than a rigid switch. You also notice those things when you look at products from other companies that are selling well. I was certainly giving them the non-Japanese perspective that I was asked to provide. But that wasn’t all, I was also going as far as to consider what the user would be satisfied with when doing Seihin Shinsa of the product. I believe that is the view of Konosuke Matsushita and the value of Panasonic. I saw most of the Panasonic Group’s sites, and nearly all of its products. All of their products are consistent in that they are safe and secure at a basic level, in addition to being durable, satisfying to users, and enriching their lives. I make sure that all of that is in order, that the products pass their reviews, and that they then reach the people of the world with their quality intact. That's what makes my current job so rewarding.”
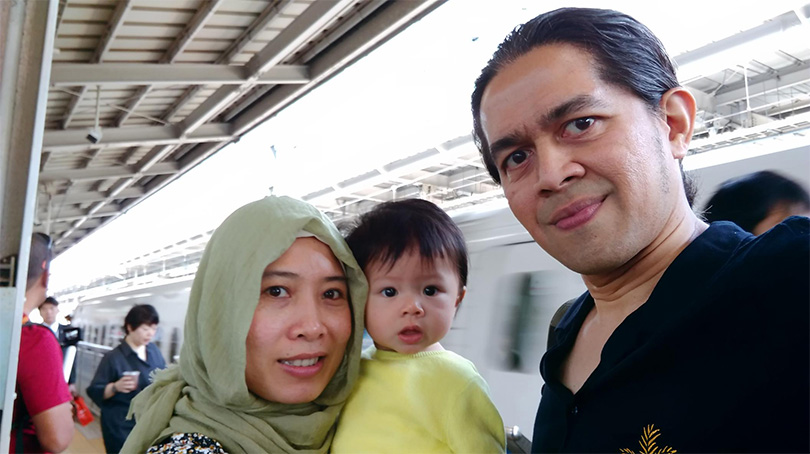
His child was born in Japan. He also often went on family trips.
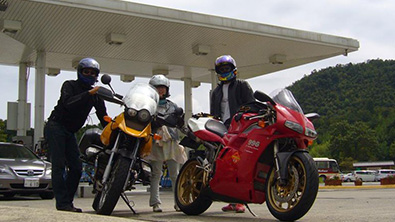
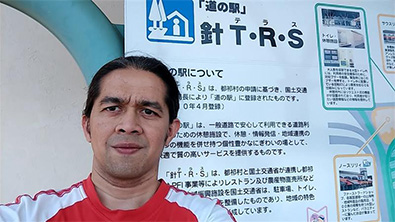
Motorcycling is his hobby. He also enjoys touring with other motorcycle enthusiasts.
Having hope for a network to spread the value of Panasonic to the world
“I got a job at Panasonic, and many of the alumni supported by the Panasonic Scholarship work for various Japanese companies, that is, other manufacturers, as well as companies both at home and abroad all over the world. This is a common surprise for alumni and something for which we are all eternally grateful. The source of the scholarship is the company's profits. It's being used to help Asian students who have nothing to do with the company. Perhaps the value of this support is only known to those of us who have received it. However, this value is deeply connected to the ideas of Konosuke Matsushita. That's the exact value of Panasonic that I've been talking about. With the idea of ‘devoting ourselves to the progress and development of society and the well-being of people to enhance the quality of life throughout the world’ as stated in Panasonic's manifesto, we alumni practice in every part of the world to pay close attention to our own work, to sufficiently fulfill our roles, and to live and work in ways that inspire us. As each of us looks back on our lives, we can see a common starting point along the way: the Panasonic Scholarship.”
Mr. Muzafar has also worked to build a network with many alumni, in addition to alumni from his cohort. By continuing to grow this network in the future, he hopes to deepen ties with people around the world who share Panasonic's values. Now, with Asian Panasonic Scholarship scholars and alumni studying in their home countries without studying in Japan, Mr. Muzafar says that he is also looks forward to the possibility of understanding Japanese culture as well as a mutual understanding of different cultures, leading to the cultivation of new values.