Environment : Business of Factory Energy Conservation Support Service
Environmental Support for the Entire Factory
Panasonic launched its Factory Support Service Business in April 2010, by making use of actual results in reducing CO2 emissions in production activities in the three years of fiscal 2008-2010. This service provides all-round support in energy-saving activities at factories, from visualization of energy use and energy efficiency diagnoses to execution of concrete energy efficiency measures, covering the aspects of technology, facility and equipment, human resources, and finance.
As part of this service, we have analyzed data which are managed by respective our customers, and understood the level of energy consumption efficiency with basic energies such as electricity and gas used in respective factories, physical data such as energy flow, pressure, temperature, and humidity that directly reflects the operation status of the facility and equipment. With the analysis results, we have supported the customers in swiftly formulating energy efficiency measures, making trial calculations, and improving accuracy of the verification.
At the beginning when the business started, we worked to clearly understand deterioration of equipment and necessity of its maintenance, through indicating variations of energy efficiency in long term in graphic displays with power equipment such as compressors, boilers, and freezers, and reduced their wasted energy consumption. Then, we accelerated energy efficiency activities, through paying attention to the production volume per basic unit calculated from the production volume and energy consumption, and utilizing the production volume per basic unit to "CO2 ITAKONA method" which timely extracts issues of production lines, and of facilities and equipment.
From fiscal 2020, we have further updated our activities; we have started the "Factory support service business" that formulates activities and plans for improvement in all of the areas related to the customer’s environmental sustainability management, including "energy-saving", "new energy and energy creation", "resource circulation" and "risk management."
In a contribution outside the company, in the 13 years from 2010 to 2023, we conducted diagnosis for approximately 789 cases, and provided energy-saving and factory support in the automotive-related, food, pharmaceutical, machinery, and electronic components industries in Japan. Moreover, we registered as a diagnostic service body dedicated to corporate energy efficiency diagnosis for 'Support for High-efficiency Installations for Facilities with Targets' led by the Ministry of the Environment, which provides information on the use of effective facilities and equipment, operational improvements, and the like, in order to reduce CO2 emission. We continue these energy efficiency activities.
By making full use of environmental technologies, know-hows, and experience which have been developed and established in Panasonic group, the service of the Total Environmental Package Solutions for Entire Factory, which provides a total solution that covers not only energy efficiency measures, but also environmental and energy technologies in wastewater treatment and drainage and water recycling, exhaust gas treatment, resources recycling, soil and groundwater purification, and photovoltaic power generation, has been developed. By enhancing the package service, we will further contribute to the comprehensive environmental solutions for Panasonic customers.
Panasonic Energy Co., Ltd. Mobility Energy Business Division - smart EMS installation at Suminoe Factory
In fiscal 2021, we installed "Smart EMS Energy-saving Automated Control(*1)" that the Panasonic Holdings Corporation Manufacturing Innovation Division has developed and is promoting , collaborating with the Mobility Energy Division at the Suminoe Factory of Panasonic Energy Co., Ltd, and we are now conducting verification of the energy-saving effect.
In the manufacturing process for the polar plates for batteries, it is necessary to maintain a low humidity environment in order to secure the manufacturing quality, and this consumes a large amount of energy for air conditioning. By using the smart EMS's energy-saving automatic control instead of the conventional manual control to maintain steady conditions, it is possible for the autonomous control using AI to optimally follow the fluctuations in the required load, which arise due to the processing conditions and the variation in the external air temperature in different seasons. This realizes air conditioning control without excess or deficiency.
Thanks to the installed smart EMS, the CO2 emissions in the processes concerned was reduced by approx. 5.9% which exceeds the target of 4.8% in the winter months. From now on, we will continue the verification in the intermediate periods and summer months in preparation for full utilization, with the aim of achieving an energy-saving effect of a 13.7% reduction in CO2 emissions throughout an entire year.
Our company will roll out this technology widely and globally to other sites to contribute to the CO2 reduction activities in the Panasonic Group.
(*1. Smart EMS: Received Energy Conservation Grand Prize 2018 Minister of Economy, Trade and industry Prize (Energy savings category))
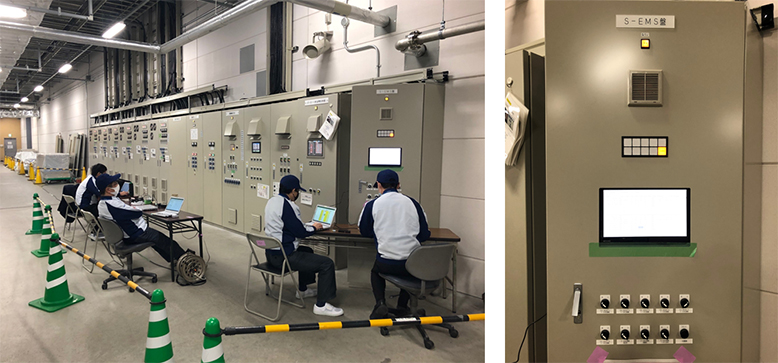
Construction of RE100 Demonstration Facility at the Kusatsu Factory, Electric Works Company, Panasonic Corporation
In FY 2021, our company contributed to the launch of the H2 KIBOU FIELD demonstration facility at the Kusatsu Factory (Electric Works Company, Panasonic Corporation). This facility combines pure hydrogen fuel cells (495 kW), solar cells (approximately 570 kW), and storage batteries (approximately 1.1 MWh) to provide a RE100 solution that uses 100% renewable energy for energy consumption in business activities.
The H2 KIBOU FIELD is a facility for achieving RE100 for the electric power used by the manufacturing department in the factory, as well as for developing and verifying technologies for optimal power supply and demand operation through coordination of three batteries.
From the initial stage of consulting, we examined the configuration of solar cells and storage batteries, and conducted simulations of power supply and demand in combination with fuel cells. We designed the facility to enable a wide range of demonstrations. In addition, we were able to successfully complete the world’s first demonstration facility by building on design and construction know-how through legal compliance with relevant ministries and agencies based on full-scale use of hydrogen power generation and coordination with hydrogen suppliers and electric power suppliers.
Utilizing this experience, we will continue to implement prompt and optimal proposals and construction both inside and outside the company.
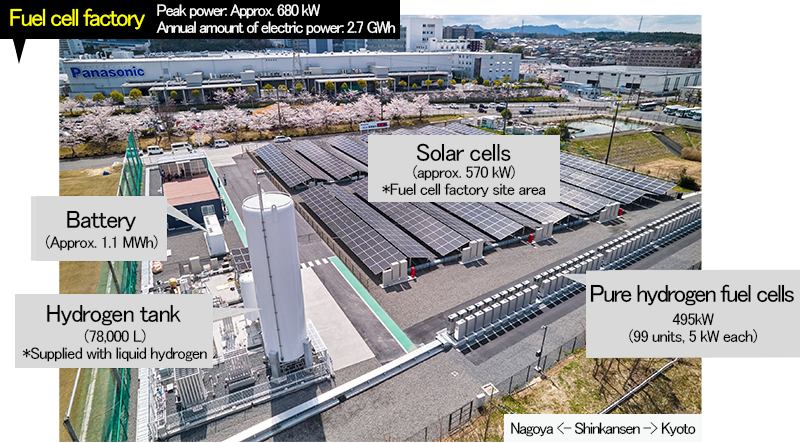